МАТЕРИАЛОВЕДЕНИЕ
УДК 621.91.762
А. И. Саградян
Исследование деформированного состояния приконтактных
слоев
инструмента при обработке конструкционных материалов
(Представлено академиком Л. А. Агаловяном 7/ VII 2005)
Решение проблемы износостойкости инструмента
связано с изучением закономерностей процесса резания в зоне контактного
взаимодействия. Одним из дополнительных резервов повышения износостойкости
инструмента в процессе резания является управление взаимодействием дефектов
кристаллической решетки поверхностных слоев инструментального материала. В этой
связи наибольший интерес представляeт исследование структурных изменений при
резании [1-6].
Экспериментальноe
исследование изменения структуры в процессе резания в материаловедческом аспекте
позволяет определить структуру поверхностей трения, ее влияние на
износостойкость инструмента и дать структурную оценку трущихся пар резец -
обрабатываемая деталь при пластическом деформировании их поверхностных
слоев.
Целью данной работы является
исследование структурных изменений на контактном участке поверхностных слоев
инструмента вследствие действующих давлений, температур, контактных напряжений и
деформаций. В условиях длительного воздействия температуры и давления
физико-механические свойства деформированных материалов релаксируют. В работе
рассматривается это явление, а также воздействие нормальных и касательных
напряжений на свойства поверхностных слоев инструментального
материала.
Эксперименты проводились на станке
1К62 с вариатором ВР-1 для плавного регулирования скоростей, при режимах
резания, соответствующих 60-минутной стойкости инструмента, которые для пapы
B14M7K25-сталь 45 составляли: V60 = 65 м/мин, S = 0.3 мм/об, t = 2 мм
[2].
Идентичные условия термообработки всех
исследуемых резцов и тщательный контроль на всех стадиях их изготовления
обеспечили незначительный разброс стойкости инструмента. Были исследованы три
одинаковых по физико-механическим свойствам резца так, чтобы можно было рельефно
представить все три стадии износа, как при работе одного резца. Первый из них
работал до конца приработки, т.е. самоорганизации и стабилизации процесса,
второй - с начала до конца установившегося периода износа, а третий - с начала
до полной потери работоспособности. Для каждой стадии износа испытывались по три
резца и выбирались средние значения результатов
эксперимента.
Для изучения структуры
применены металлографические и рентгеноспектральные методы с использованием
микроскопа МИМ-8И и рентгеновского микроанализатора INCA Energy 400,
установленного на сканирующем электронном микрозонде VEGA-TS5130MM с разрешающей
способностью 1мкм. Для изучения изменений структуры контактных слоев в теле
резца измерялась микротвердость в исследуемых сечениях шлифов режущего клина с
помощью микротвердомера ПМТ-3.
Важное
значение с точки зрения стойкости инструмента имеет исследование структурных
превращений на разных стадиях износа в зависимости от продолжительности работы
резца и связанных с ним явлений, происходящих на контактных поверхностях
инструмента вследствие воздейстия на них высоких давлений и температур. При этом
происходят необратимые структурные превращения, а точки фазовых превращений, в
частности a ® g, перемещаются в сторону малых температур [4,
5].
Для исследования
напряженно-деформированного состояния на передней поверхности инструмента
изучено воздействие контактных напряжений [4], экспериментально подтверждено
наличие двух участков в зоне контакта при резании - пластического и упругого
(рис. 1,2).
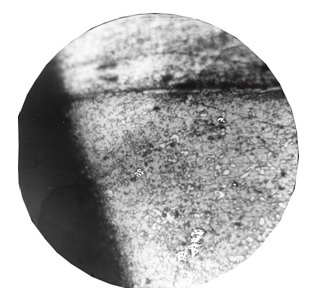
|
Рис.1. Конфигурации застойного и белого слоев по ширине
контакта
в зависимости от касательных
напряжений.
Область
пластического контакта разделена на две части: C2 - участок
деформационного упрочнения, (C1-C2) - участок
температурного разупрочнения (рис. 2).
Рис. 2. Изменение толщины застойного и белого слоев в
зависимости
от касательных напряжений по ширине контакта.
На участке упругого контакта (0 < x <
(C - C1)) касательные и нормальные напряжения
меняются пропорционально [3]:
где mF - коэффициент внешнего трения, sN - нормальное напряжение:
где s
M - нормальное контактное напряжение у режущей
кромки, x - расстояние рассматриваемой точки передней поверхности от точки
отрыва стружки, c - ширина контакта стружки с передней поверхностью, n -
показатель степени, характеризующий неравномерность распределения
напряжений.
Значения sM и n рассчитываются по формулам [3]
sM = |
N
bc
|
|
м н о |
|
rc
ax[m + tg(b - g)]
|
+ 1 |
ь э ю |
, n = 2 |
м н о |
|
c
ax[m + tg(b - g )]
|
- 1 |
ь э ю |
, | |
(3) |
где N - нормальная сила (N = 1580 H),
r - расстояние текущей точки от начала координат, a и b - толщина и ширина
среза, c - ширина контакта, x - усадка стружки, b - угол сдвига, g - передний угол,
m - средний коэффициент трения по всей длине
контакта.
Согласно условиям наших
экспериментов: r = 2 мм, m = 0.8, x = 2.95, b = 30o, g = 10o, a = 0.21мм, b = 2.83 мм, c = 1.99 мм -
получаем: sM = 1828 МПа,
n = 3.54.
Определив sM и n, можно построить эпюру распределения
нормальных и касательных напряжений на передней поверхности
резца.
Длина пластического контакта
C1, рассчитанная согласно [3]:
C1 = a[x(1 - tgg) + secg], | |
(4) |
составляет: 0.75
мм.
Из рис. 2 значение коэффициента трения
m можно рассчитать как
m = (mDnC2 + mDn(C1-C2)) + mDy(C-C1) или m = |
ж з и |
|
tDnC2
sN
|
+ |
tDn(C-C2)
sN
|
|
ц ч ш |
+ |
tFy(C-C1)
sN
|
, | |
(5) |
где tDnC2, mDnC2, tDn(C-C2),
mDn(C1-C2) и tDy(C-C1),
mDy(C-C1) - касательные напряжения и коэффициенты
трения, соответственно, на участках C2, (C1-C2) и (C-C1).
Для нашего случая: C2 = C1/2 = 0.375 мм, а длина упругого
контакта - (C-C1) = 1.25
мм.
Уравнение (5) подтверждается
экспериментально (рис. 1, 2); из него следует, что касательные напряжения в
отличие от принятой модели [3] при обработке малоуглеродистых сталей на участке
пластического контакта меняются по параболическому закону, увеличиваясь от
начала режущего лезвия до конца участка деформационного упрочнения C2
и несколько снижаясь на участке температурного разупрочнения (C1-C2). Эти же напряжения на участке упругого
контакта имеют гиперболическую зависимость, коррелируя с нормальными
напряжениями (рис. 2).
Изменение нормальных
напряжений s
N по длине контакта с передней
поверхностью инструмента описывается гиперболической зависимостью. В [1, 3] на
участке пластического контакта в основном принимается tF = tS, т.е.
касательные напряжения постоянны.
Проведенные исследования экспериментально подтверждают качественное
различие кинематических процессов и деформационного состояния на двух участках
пластической зоны контакта (рис.1). Изменение касательных напряжений в этой зоне
зависит от суммарного эффекта двух конкурирующих процессов: деформационного
упрочнения и температурного разупрочнения (рис. 1,
2).
Под воздействием нормальных и касательных
напряжений, а также давлений и температур на передней поверхности, и особенно на
участке пластического контакта, наблюдается деформационное упрочнение тонких
поверхностных слоев инструментального материала в результате концентрации
дислокаций с повышением их плотности на расстоянии 25...45 мкм от контактных
поверхностей (передней и задней) (рис. 3). На глубине 15...20 мкм наблюдается
вторая граница концентрации дислокаций, что, по-видимому, является результатом
волнового характера распределения деформаций с поверхности контакта в тело
инструмента. Таким образом, в низлежащих слоях толщиной до 60 мкм происходит
волновой процесс распределения деформаций, связанный с воздействием сходящей
стружки, что и приводит к стpyктypным изменениям этих
слоев.
Распределение плотности и концентрация
дислокаций отражают влияние давлений со стороны передней и задней поверхностей
инструмента, и линия приобретает вид кривой, показывающей распределение
деформаций нa стадии установившегося износа - T2 (рис.3, 4, г) в
режущем клине резца.
Под влиянием указанных
факторов в процессе резания формируются поверхностные слои твердых тел,
обуславливающие механизм трения и износа при резании, отличающийся специфическим
структурным состоянием.
Образующиеся в
процессе трения поверхностные слои инструмента, особенно на участке
пластического контакта, характеризуются повышенной свободной энергией,
физической и химической активностью, а также вариацией механических свойств по
сравнению с низлежащими слоями, не участвующими в процессе контактирования.
Поверхностные слои определяют механизм контактного взаимодействия и уровень
износостойкости инструментального материала, что свидетельствует о специфическом
влиянии и роли пластической деформации поверхностных слоев на изменение структур
приконтактных слоев.
Глубина структурных
изменений в поверхностно-деформированном слое в наших экспериментах,
определенная измерениями микротвёрдостей (рис.4), составляет ~
100...150 мкм, о чем свидетельствует также рентгеноспектральное
зондирование по сечению режущего клина инструмента (рис. 3).
Поверхностные эффекты в [5] объясняются
образованием в поверхностной области контакта слоя с повышенной плотностью
дислокаций, который является барьером для дислокаций, генерируемых в процессе
деформации.
Согласно [5] определено
действующее на дислокации эффективное напряжение t:
где ta - внешнее напряжение, ti - обратное напряжение, возникающее в результате
пластической деформации внутренних слоев. Дополнив t
величиной tS, получим
где
tS - внутреннее напряжение, создаваемое
debirs-слоем (слоем с повышенной плотностью
дислокаций).
Энергия активации пластической
деформации U связана с напряжением деформированного приповерхностного слоя:
U = U0 - Vat =
U0 - Va(ta - ti - tS). | |
(7) |
Отсюда видно, что при постоянном активационном объеме Va и
уменьшении tS энергия активации U также
уменьшается. При этом активационный объем также является функцией tS, т.е.
Va = KTDln /Dt = KTD ln/[Dta - D(ti + ts)], |
|
(8) |
где
- скорость деформаций.
При этом в качестве критерия, оценивающего степень изменения структуры и
свойств инструментального материала, было выбрано изменение значения
микротвердости режущего инструмента в разные периоды работы
резца.
Микрошлифы были изготовлены в
сечениях, нормальных к главной режущей грани, в центре активной части режущей
кромки, совпадающей примерно с центром лунки.
При рассмотрении поля микротвердости исходя из продолжительности работы
резца видно, что структура инструментального материала претерпела изменения, так
как в конце стадии начального износа микротвердость на непосредственном контакте
со сходящей стружкой повышается по сравнению с матричной на 110...130 HV (рис.4,
а). Причем граничное измерение микротвердости от передней поверхности примерно
совпадает с линией распределения деформации со стороны как передней, так и
задней поверхностей. На участке пластического контакта C1, где
действуют наибольшие нормальные и касательные напряжения, экспериментально
обнаружено (рис. 4, а), что на глубине до 100 мкм в конце стадии начального
периода износа уровень микротвердости доходит до 1166 НV. В конце стадии
установившегося износа резца замечено некоторое снижение микротвердости, однако
на упругом участке контакта сохраняется высокая микротвердость - до 1000 HV,
мало отличающаяся от матричной, составляющей 1030...1050 HV. Как показали
экспериментальные данные, на участке пластического контакта повышение
микротвердости по сравнению с матричной составляет до 130 НV и сохраняется на
полочке контакта практически до 55 мин работы инструмента, при этом сохраняются
высокие физико-механические свойства. Причем по сравнению с обычными
быстрорежущими сталями зона нормального периода работы у резцов из
быстрорежущего сплава с интерметаллидным упрочнением В14М7К25 на 5 мин больше,
что при скоростях 60-минутной стойкости, превышающих в 1.5 раза обычные
быстрорежущие стали, обеспечивает высокую производительность, качество
обработанных поверхностей,
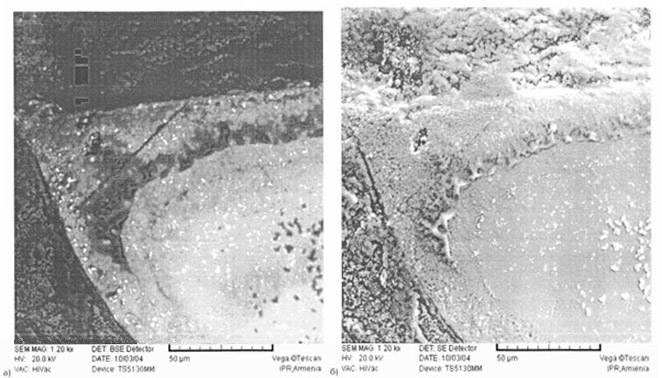 |
Рис.3. Распределение плотности
дислокаций в теле инструмента: а)сканирование
по глубине, б) сканирование по
площади
Рис.4. Зависимость микротвердости от продолжительности
работы резца при обработке стали 45
резцами В14М7К25 в режимаx:
V60 = 65 м/мин., S = 0.3 мм/об., t = 2.0 мм: а) в конце начального
износа,
б) в конце установившегося износа, в) в стадии катастрофического износа, г)
зависимость
износа от продолжительности, по стадиям.
долговечность инструмента и низкую себестоимость
обработки.
Обнаружено, что распределение
плотности и концентрация дислокаций отражают влияние давлений и температур со
стороны передней и задней поверхностей инструмента, показывающиx глубину и
конфигурацию прилегания дeформаций в теле резца. Установлено, что с повышением
деформированного состояния поверхностных слоев инструмента и вследствие
изменения структуры и микротвердости при соответствующих условиях резания
повышается износостойкость инструмента.
Государственный инженерный университет Армении
Литература
1. Полетика М. Ф. - Контактные
нагрузки на режущих поверхностях инструмента. М. Машиностроение. 1985. 160 с.
2. Саградян А. И., Саркисян К. А. - Межвуз. сб. науч. трудов "Машиностроение". Ереван. Cер. 16. Bып. 3.
1980. С. 29-35.
3. Зорьев Н. Н. - Развитие науки о резании металлов. М. Машиностроение. 1967. 405 с.
4. Скотникова М. А., Касторский Д. А.,
Строкина Т. И. - Инструмент и технология. 2002. №7-8. C. 62-68.
5. Рыбакова Л. М., Кусенкова Л. И. - Структура и износостойкость металлов. М. Машиностроение. 1982. 209 с.
6. Галкин С. Г. - B сб.:
Судостроение и судоремонт. СПб. 1998. C. 148-151.